Services
Quality Assurance Inspection Services
SORSYS Inspection Services: Quick, Cost-Effective, and Expert Sorting
SORSYS offers sorting and inspection services for all your parts. Our high-tech machines make sure every piece meets your needs. Plus, we do everything right here in our own facility.
Stop Losing Money! Automate Your Inspection Process Today.
What We Offer:
Expert Inspection and Sorting: Our top-notch machines quickly find any problems, making sure every part is just right.
Pack It Up, Mark It Up: After checking, we pack everything based on your instructions and label it for easy tracking.
We Stick to the Rules: Our checks are in line with the best standards, tailored to what you need.
Fair Pricing: Costs are clear and based on how complex the sorting is and how many parts you have.
Big Capacity: We can handle 10,000 to 15,000 parts each day, so you get your parts back fast.
Why Choose In-House Services?
Zero Defects: Our AI-powered inspection guarantees precision sorting and flawless parts.
Speedy Turnaround: Get your parts sorted and back faster with our in-house process.
Save on Costs: Cut down on what you spend on labor by letting our experts do the sorting.
Leave It to the Pros: Our team knows exactly what to look for, so you get the best quality.
More Room for You: Free up space at your place for more production. We'll handle the sorting.
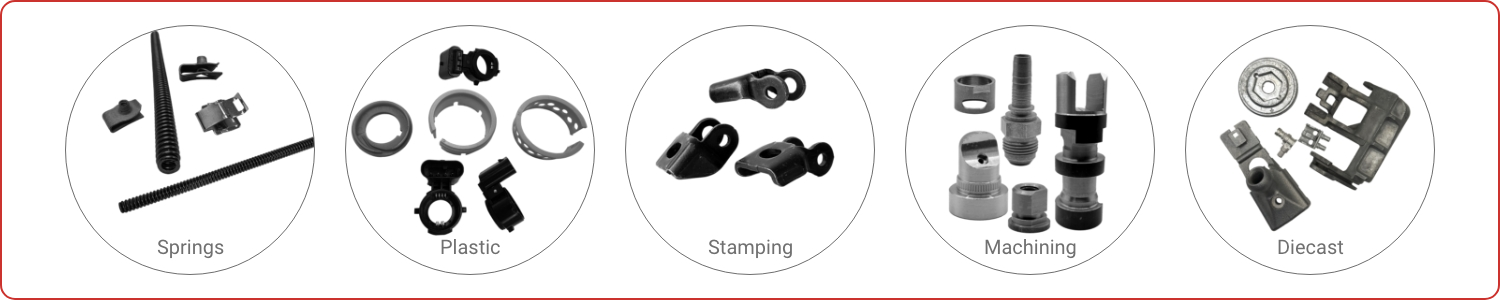
How Sorsys Technologies Ensures Quality with Advanced Inspection Solutions
Sorsys Technologies Inc. specializes in high-precision inspection solutions designed to help manufacturers maintain strict quality control. With advanced automated inspection machines, Sorsys ensures that defective parts are identified and sorted efficiently, minimizing waste and improving production efficiency.
How the Inspection Process Works
1. Sorting Request Received
The inspection process begins when a client submits a sorting request. This request outlines the specific inspection criteria, including the types of defects to be detected and the acceptable quality levels for production.
2. Providing Sample Parts
To ensure an accurate and efficient inspection process, Sorsys requires both good and defective parts from the client. These samples serve as reference points to fine-tune the inspection parameters and optimize defect detection accuracy.
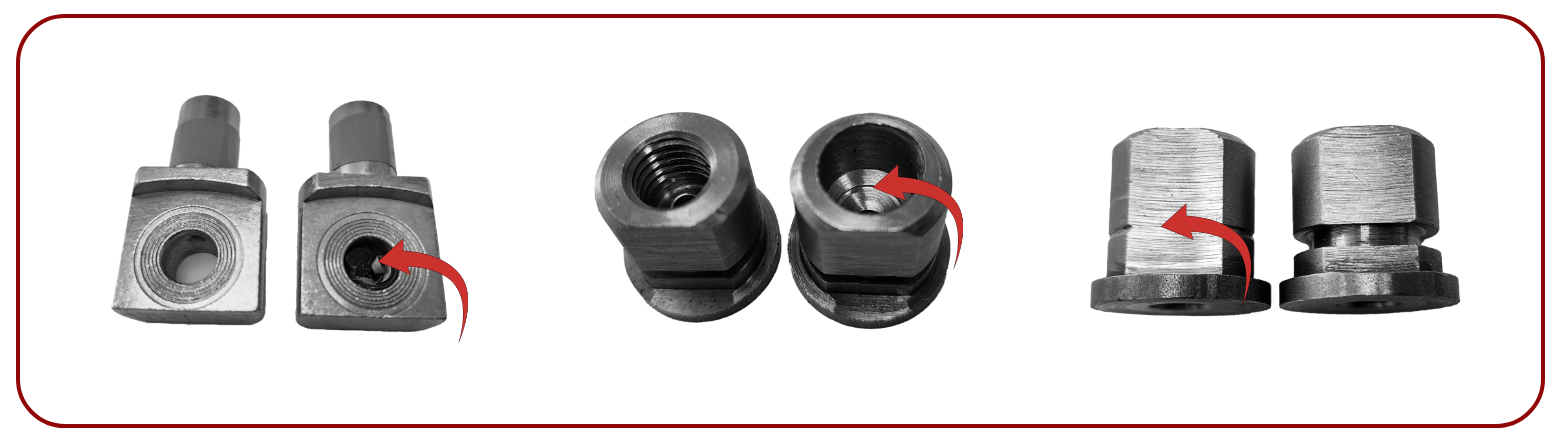
3. Defining Inspection Criteria
Before inspection begins, Sorsys works with the client to establish clear inspection criteria. This includes:
Minimum defect size: The smallest imperfection that needs to be detected.
Types of defects: Including burrs, cracks, missing features, contamination, discoloration, and more.
Red Rabbit Samples: A minimum of three known defective parts per defect type is required to train the system accurately.
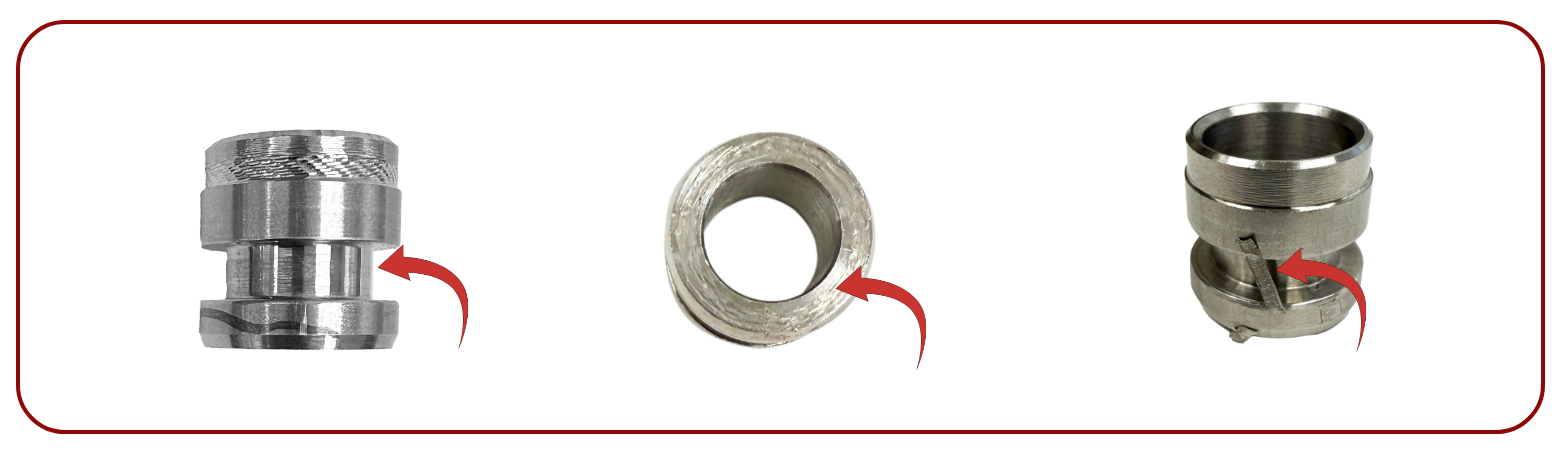
4. Conducting a Feasibility Study
A crucial step in the process is the Feasibility Study, where Sorsys evaluates the feasibility of inspecting the client's parts based on the given criteria. The study includes:
Detection capability: Ensuring the system can reliably detect and differentiate defects.
Sorting capacity: Estimating the speed and volume of parts that can be inspected.
Cost per unit: Determining the cost-effectiveness of the inspection process.
5. Machine Setup and Testing
.jpg)
Once the Feasibility Study is completed and approved, the Sorsys inspection machine is set up to begin testing. This includes:
Calibrating sensors and cameras for optimal visibility.
Running sample tests to validate defect detection accuracy.
Adjusting settings based on initial test results to maximize efficiency.
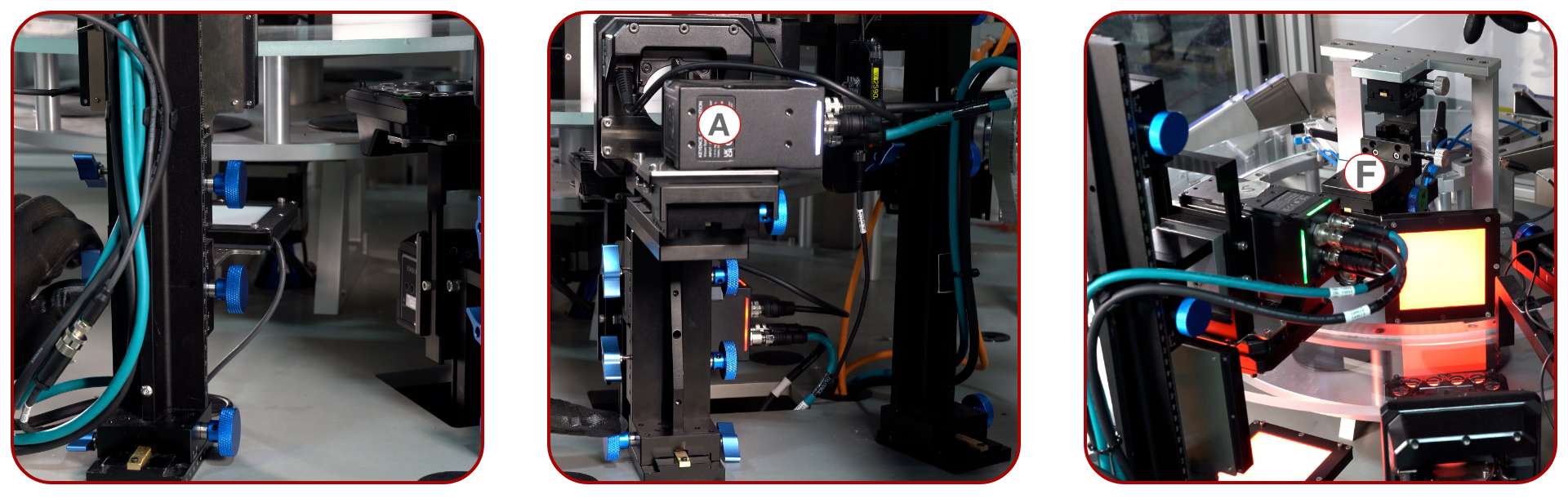
6. Inspection and Sorting Process
With everything in place, the automated inspection begins. The machine scans each part, identifying and separating defective pieces from good ones in real-time. This ensures only high-quality parts move forward in production.
7. Reporting and Finalization
After sorting is complete, Sorsys provides a detailed Feasibility Study Report, which includes:
Data on defect detection success rates.
Sorting efficiency and throughput metrics.
Overall cost analysis per inspected unit.
Recommendations for further process improvements if needed.
We Inspect a Variety of Parts & Defects: Machining, Diecasting, Stamping, Springs, and Plastic Injected Parts.
Defects including but not limited to: Missing features (e.g., threads ID and OD), burrs, chips, contamination, oversize and undersize issues, surface damage (dent, scratch, hit mark, saw mark), poor fill in diecast parts, discoloration, and mixed parts.