AI Powered Visual Inspection
Visual inspection machines have become essential tools in modern manufacturing, greatly enhancing quality control processes. Equipped with multiple cameras and AI-powered analysis, these machines are capable of inspecting products with unparalleled accuracy. By employing high-resolution cameras positioned at various angles, visual inspection systems capture detailed images of parts as they move along production lines. This multi-angle approach ensures thorough examination of every product, leaving no detail unchecked.
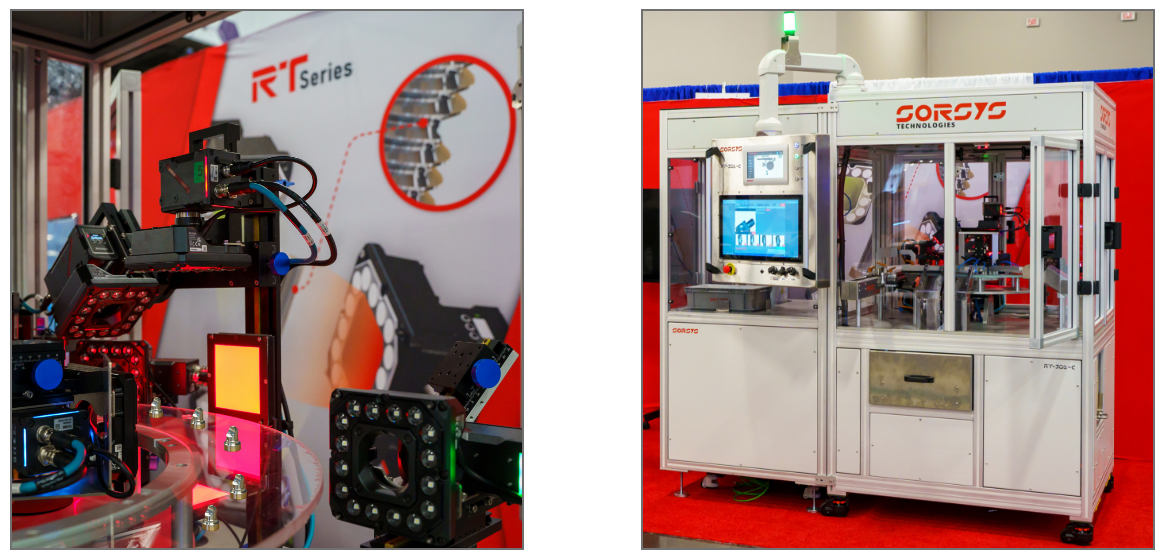
AI plays a crucial role in processing these images. Deep learning algorithms, such as Convolutional Neural Networks (CNNs), are used for tasks like object detection, defect recognition, and classification. These algorithms, trained on vast datasets, excel at identifying defects such as scratches, cracks, or misalignments with great precision. AI’s adaptability also allows these systems to continuously improve over time, making them more effective at detecting new or previously unseen defects.
Sorsys Technologies, a company that specializes in automated visual inspection, offers advanced solutions that incorporate AI for defect detection across various industries, such as automotive and electronics. Their machines, like the RT-Series, utilize multi-camera systems and AI to detect issues like missing features, burrs, chips, and surface damage. The incorporation of AI accelerates inspection processes and provides more consistent results compared to traditional manual methods.
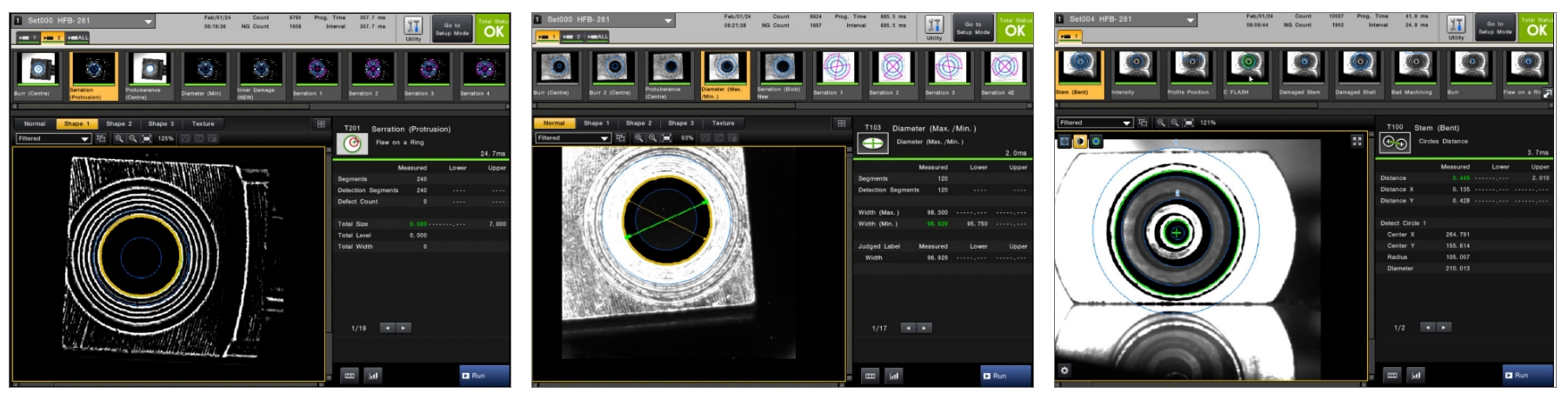
The integration of AI in visual inspection goes beyond defect detection—it allows for real-time analysis. Manufacturers can detect and resolve issues during production, reducing waste and ensuring that high-quality standards are consistently met. This capability is particularly critical in sectors where precision is paramount, such as aerospace and medical device manufacturing.
Emerging advancements in AI, such as transfer learning and edge computing, have further enhanced the capabilities of visual inspection machines. These innovations enable models to be trained on smaller datasets and allow for faster processing times, making real-time decision-making on production lines more efficient. As a result, manufacturers are able to adapt these systems across various sectors, from aerospace to agriculture, ensuring accurate and reliable defect detection.
By integrating multi-angle cameras and AI, manufacturers not only boost throughput and ROI but also enhance the reliability of their quality control processes. These systems are particularly advantageous for industries that require continuous monitoring of production lines to ensure defective products are caught before reaching the market.
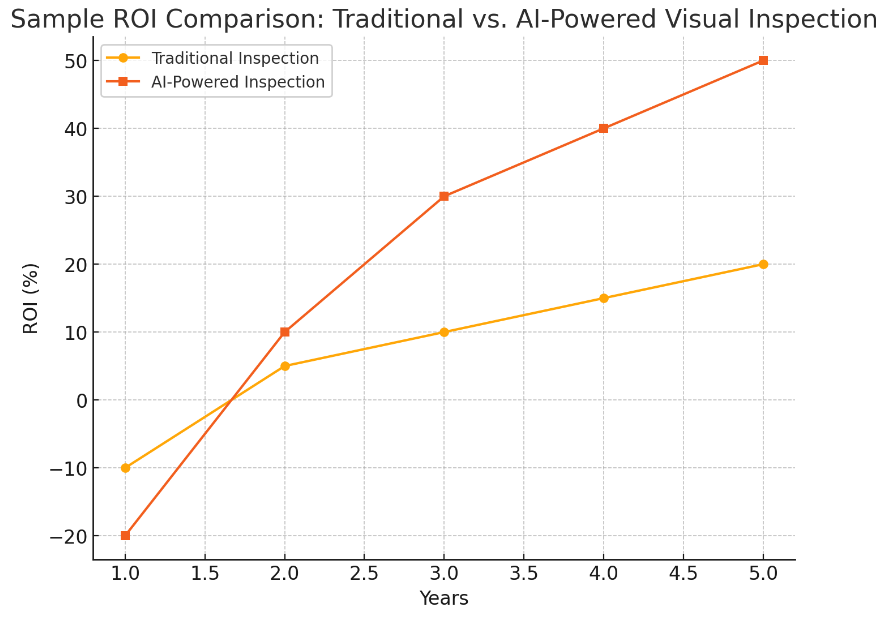
In conclusion, AI-powered visual inspection systems with multi-angle cameras are transforming quality control across industries by providing faster, more accurate, and consistent results. These systems allow manufacturers to detect defects in real-time, reducing waste, improving efficiency, and ensuring that products meet the highest quality standards.
If you're a part manufacturer looking to enhance your inspection process, Sorsys Technologies offers tailored solutions. You can choose our in-house inspection services, or alternatively, you can buy or lease one of our advanced inspection machines. Our technology ensures you achieve the highest level of precision and efficiency for your production line.
In the fast-paced and ever-evolving world of modern industry, precision and efficiency are paramount.
One of the critical components ensuring these qualities in manufacturing and production is the inspection machine. These sophisticated devices play a crucial role in maintaining high standards of quality, safety, and reliability across various industries, including automotive, electronics, pharmaceuticals, food and beverage, and aerospace.
What is an Inspection Machine?
An inspection machine is a device or system designed to automatically examine products, components, or materials to ensure they meet specified quality standards. These machines use a variety of techniques, including visual inspection, dimensional measurement, surface defect detection, and chemical analysis, to detect flaws, inconsistencies, or deviations from the required specifications.
Types of Inspection Machine
Visual Inspection Machines: These use cameras and image processing software to detect surface defects, misalignments, or assembly errors. Commonly used in electronics and automotive industries, these machines can identify issues such as scratches, dents, or improper labeling.
Dimensional Inspection Machines: These systems measure the physical dimensions of products to ensure they comply with design specifications. They employ tools like calipers, micrometers, and coordinate measuring machines (CMMs) to provide precise measurements.
X-ray Inspection Machines: Utilizing X-ray technology, these machines can see through materials to identify internal defects such as cracks, voids, or foreign objects. This technology is widely used in the food industry to detect contaminants and in the electronics industry to inspect solder joints.
Optical Inspection Machines: These devices use light, often lasers, to scan products and detect surface defects or measure dimensions. They are highly effective in inspecting high-precision components such as semiconductor wafers.
Automated Optical Inspection (AOI) Systems: AOI systems are prevalent in the electronics industry, where they inspect printed circuit boards (PCBs) for defects like solder bridges, missing components, or incorrect placements.
Pharmaceutical Inspection Machines: These specialized machines ensure that pharmaceutical products meet stringent safety and quality standards. They inspect aspects like tablet weight, size, shape, and packaging integrity.
Benefits of Using Inspection Machines
Increased Efficiency: Automated inspection machines significantly speed up the inspection process, allowing for rapid detection and correction of defects without slowing down production lines.
Enhanced Accuracy: These machines provide a level of precision and consistency that is difficult to achieve with manual inspection. This leads to higher quality products and reduces the likelihood of defects reaching the customer.
Cost Savings: By identifying defects early in the production process, inspection machines help prevent costly recalls and rework. This not only saves money but also protects the brand’s reputation.
Compliance with Standards: Many industries are subject to stringent regulatory standards. Inspection machines ensure that products comply with these standards, thereby avoiding legal and financial repercussions.
Safety: In industries such as food, pharmaceuticals, and aerospace, ensuring product safety is paramount. Inspection machines help detect potential safety hazards, ensuring that only safe products reach the market.
The Future of Inspection Machines
The future of inspection machines is closely tied to advancements in technology. Artificial intelligence (AI) and machine learning are set to revolutionize the inspection process by enabling machines to learn from past data and improve their accuracy and efficiency over time. Additionally, the integration of the Internet of Things (IoT) will allow inspection machines to communicate with other devices on the production line, leading to more coordinated and efficient operations.
Moreover, the development of more advanced sensors and imaging technologies will enable inspection machines to detect even the smallest defects and ensure the highest quality standards. The use of augmented reality (AR) and virtual reality (VR) could also enhance the inspection process by providing operators with real-time, detailed views of the products being inspected.
Conclusion
Inspection machines are an indispensable part of modern manufacturing and production. They ensure that products meet the highest standards of quality and safety, which is crucial in today’s competitive and regulated markets. As technology continues to advance, these machines will become even more sophisticated, further enhancing their ability to detect defects and improve overall efficiency. Investing in state-of-the-art inspection machines is not just a matter of staying competitive; it is a commitment to excellence and customer satisfaction.
The Role of Vision Inspection Systems
In the era of rapid technological advancements, maintaining high-quality standards in manufacturing processes is more critical than ever. Vision inspection systems, utilizing advanced imaging and processing technology, have become a cornerstone in quality assurance across various industries, including die casting and pharmaceuticals. These systems not only enhance product quality but also streamline production processes, ensuring efficiency and accuracy.
What is a Vision Inspection System?
A vision inspection system is a sophisticated technology that uses cameras, imaging software, and computational algorithms to examine products for defects, measure dimensions, and verify assembly integrity. These systems are capable of detecting minute discrepancies that might be missed by human inspection, ensuring that only products meeting stringent quality criteria reach the market.
Applications in Die Casting
In the die casting industry, precision is paramount. Components produced must adhere to exact specifications to function correctly in their applications, often in automotive, aerospace, and consumer electronics sectors. Vision inspection systems are invaluable here for several reasons:
Defect Detection: Die casting often involves complex shapes and fine details. Vision inspection systems can detect surface defects such as porosity, cracks, and incomplete filling. These defects, if unchecked, can lead to part failure in critical applications.
Dimensional Accuracy: Ensuring that the cast parts meet precise dimensions is crucial. Vision systems can measure intricate dimensions quickly and accurately, comparing them against CAD models or pre-set specifications.
Surface Finish Quality: The surface finish of die-cast parts can significantly impact their performance and aesthetic appeal. Vision systems inspect the surface texture, ensuring it meets the required standards.
Applications in the Pharmaceutical Industry
The pharmaceutical industry demands rigorous quality control to ensure the safety and efficacy of its products. Vision inspection systems play a vital role in several areas:
Packaging Inspection: Ensuring the integrity of packaging is essential to protect pharmaceutical products from contamination. Vision inspection systems check for correct labeling, seal integrity, and packaging defects such as incorrect printing or damaged boxes.
Tablet and Capsule Inspection: Consistency in shape, size, and color of tablets and capsules is critical. Vision systems can sort out defective products, ensuring uniformity and adherence to pharmaceutical standards.
Fill Level Inspection: For liquid medications, maintaining the correct fill level in each bottle or vial is crucial. Vision systems measure the fill level with high precision, ensuring that each container has the appropriate amount of product.
Benefits of Vision Inspection Systems
Increased Efficiency: Automated inspection speeds up the quality control process, reducing bottlenecks in production lines and increasing overall throughput.
Enhanced Accuracy: Vision systems provide a higher level of accuracy compared to manual inspections, significantly reducing the risk of human error.
Cost Savings: By identifying defects early in the production process, vision inspection systems help in minimizing waste and reducing costs associated with rework and scrap.
Compliance and Traceability: These systems help in maintaining compliance with industry regulations by providing detailed inspection records and traceability.
The Future of Vision Inspection Systems
The future of vision inspection systems is promising, with advancements in artificial intelligence and machine learning poised to further enhance their capabilities. AI-powered vision systems can learn and adapt to new defect patterns, improving their accuracy over time. Moreover, integration with the Internet of Things (IoT) will enable real-time monitoring and analytics, providing deeper insights into the manufacturing process and further optimizing quality control.
In conclusion, vision inspection systems are transforming quality assurance in manufacturing. By ensuring precision and consistency, these systems help industries like die casting and pharmaceuticals maintain high standards, improve efficiency, and reduce costs. As technology continues to evolve, the capabilities of vision inspection systems will only expand, driving further innovation in quality control practices.
Maximizing Efficiency and ROI with the Sorsys RT-Series and Robotic Feeder Systems in Manufacturing
As global manufacturing grows more competitive, companies are increasingly seeking technologies that boost precision, efficiency, and profitability. A critical area of focus is the inspection process, which has traditionally been handled by human operators. Today, automated systems like the Sorsys RT-Series and vision-guided robotic feeder systems have revolutionized inspection. By enhancing accuracy, speed, and cost-effectiveness, these systems provide a significant improvement in return on investment (ROI) compared to manual labor. Let’s explore how these technologies compare to human-operated methods and why they’re becoming essential for manufacturers worldwide.
Sorsys RT-Series: The Next Level of Precision
The Sorsys RT-Series is a cutting-edge inspection system designed to identify defects in die-cast and machined parts. Capable of detecting issues like missing features, burrs, chips, contamination, surface damage, and size discrepancies, the RT-Series offers an unprecedented level of precision. Unlike human inspectors, who may only sample select parts, the RT-Series inspects every part, leaving no room for defects to slip through unnoticed. This is especially important in industries where minor defects can result in costly product recalls or failures.
Additionally, the RT-Series is capable of inspecting multiple parts, making it highly effective even for lower-volume parts when combined with higher-volume manufacturing processes. This capability makes the system versatile, justifying its use across various production scales.
By automating the inspection process, the RT-Series ensures consistent quality while reducing the time required for product evaluation—a crucial advantage in high-demand industries such as automotive and aerospace, where downtime can be extremely costly.
The Role of Vision-Guided Robotic Feeders: Enhancing the Inspection Process
The efficiency of the RT-Series is further amplified when paired with vision-guided robotic feeders. These feeders autonomously deliver and position parts for inspection, sorting, orienting, and positioning each piece with incredible precision. More importantly, the use of vision-guided robotic systems enables manufacturers to easily switch between different parts without the need for expensive, custom-built feeding systems, significantly lowering changeover costs and reducing downtime during production shifts.
By automating part handling, manufacturers can eliminate bottlenecks caused by manual labor, streamlining operations and improving overall productivity. These systems also excel in identifying and removing defective parts early, preventing faulty components from advancing further in the production process.
Customization and Integration: Tailored Solutions for Every Manufacturer
At Sorsys, we understand that no two manufacturing environments are the same. That’s why we offer customized configurations of the RT-Series and robotic feeder systems, ensuring that our solutions fit seamlessly into your specific production setup. Whether you're operating in automotive, aerospace, or electronics industries, Sorsys technologies can be tailored to meet your unique inspection and automation needs.
What’s more, the RT-Series is designed to integrate smoothly with existing manufacturing infrastructure and ERP systems, enabling real-time monitoring and data collection. This integration empowers manufacturers to make smarter, data-driven decisions, enhancing both productivity and quality control on the production floor.
Accuracy and Consistency: The Automated Advantage
A standout benefit of automated inspection machines like the RT-Series is their unparalleled accuracy and consistency. Even the most skilled human inspectors are prone to fatigue and mistakes, particularly during long shifts. Over time, these limitations can lead to missed defects or errors that go undetected until much later in the production process.
Automated systems, however, operate continuously without losing precision. Equipped with state-of-the-art sensors and vision technology, the RT-Series detects even the smallest flaws, such as micro-scratches, discoloration, or surface irregularities that human inspectors may overlook. This guarantees a consistently high-quality output, boosting both customer satisfaction and brand reputation.
Moreover, the RT-Series eliminates the need for random sampling by inspecting every part, which greatly reduces the chances of faulty products reaching customers and causing costly downstream issues.
Speed and Efficiency: Reducing Cycle Times, Maximizing Throughput
Integrating robotic feeders with the RT-Series not only enhances accuracy but also dramatically increases operational speed. Robotic systems can run 24/7 without breaks, maximizing productivity. This boost in throughput allows manufacturers to inspect more parts in less time while maintaining high-quality standards.
Robotic feeders also eliminate the delays associated with manual part handling and setup, reducing cycle times in high-volume manufacturing environments. In industries like automotive and electronics, even minor improvements in cycle time can lead to significant gains in production output.
Cost-Effectiveness and Long-Term ROI: Reducing Waste and Labor Costs
While investing in advanced inspection systems like the RT-Series and robotic feeders may involve higher upfront costs, the long-term savings far outweigh the initial investment. By reducing labor costs and minimizing the need for human inspectors, automated systems can lower overall operational expenses. Additionally, these systems reduce product rework and waste by detecting defects early in the production process.
Early detection prevents manufacturers from incurring the costs of further processing or shipping faulty products, which cuts down on material waste and the likelihood of expensive recalls or warranty claims. Many automated systems, including the RT-Series, also feature predictive maintenance capabilities, enabling manufacturers to address potential equipment issues before they lead to costly downtime.
Industry Standards and Certifications
The Sorsys RT-Series is compliant with key industry certifications, such as ISO 9001, ensuring that manufacturers using the system meet rigorous quality standards. This compliance further bolsters confidence in the RT-Series' ability to deliver reliable, high-precision inspections across a range of industries.
Customer Success: Real-World Results
A leading automotive manufacturer recently implemented the Sorsys RT-Series and vision-guided robotic feeder system. Within six months, the company saw a 30% reduction in defect rates, along with a significant increase in production throughput. These improvements resulted in faster cycles, reduced waste, and overall cost savings, demonstrating the tangible benefits of adopting Sorsys technology.
Conclusion: Automation as a Strategic Asset
Transitioning from manual inspection to automated systems like the Sorsys RT-Series and vision-guided robotic feeders is more than just a technological upgrade; it’s a strategic move toward greater precision, productivity, and profitability. These systems offer unmatched accuracy, speed, and cost savings, significantly enhancing both product quality and ROI.
As global manufacturing continues to evolve, automation is becoming essential for companies seeking to maintain a competitive edge. Manufacturers that invest in automated inspection technologies not only improve operational efficiency but also position themselves for long-term success in a rapidly changing market.
Ready to transform your manufacturing process? Contact Sorsys today for a personalized consultation or schedule a demo to see the RT-Series and robotic feeder systems in action. Together, we can elevate your production efficiency, optimize quality control, and secure a more profitable future.