Integrating Vision Inspection Systems with Industry 4 and IoT
Integrating Vision Inspection Systems with Industry 4.0 and IoT: Enhancing Manufacturing Intelligence
.png)
Introduction
Manufacturing is undergoing a digital revolution. With the rise of Industry 4.0 and the Internet of Things (IoT), factories are transforming into smart, connected environments. At the heart of this transformation are technologies like vision inspection systems—automated machines capable of identifying defects in parts with high accuracy and speed. By integrating these systems with IoT frameworks, companies can dramatically increase efficiency, reduce waste, and enhance traceability throughout the production line.
The Role of Vision Inspection in Industry 4.0
Vision inspection systems, such as Sorsys Technologies' RT series, are no longer standalone machines. When paired with Industry 4.0 infrastructure, these machines become real-time quality control hubs, feeding critical inspection data directly into centralized systems. This synergy offers manufacturers a new level of control and oversight—one that's data-driven and immediate.
.png)
Key Benefits of Integration
1. Real-Time Quality Control
Instead of manual inspection that is often slow and prone to error, real-time feedback from vision systems ensures immediate detection of defects. As soon as a defect is found, the system can trigger alerts or even halt production to prevent further issues. This drastically reduces the risk of defective products reaching customers.
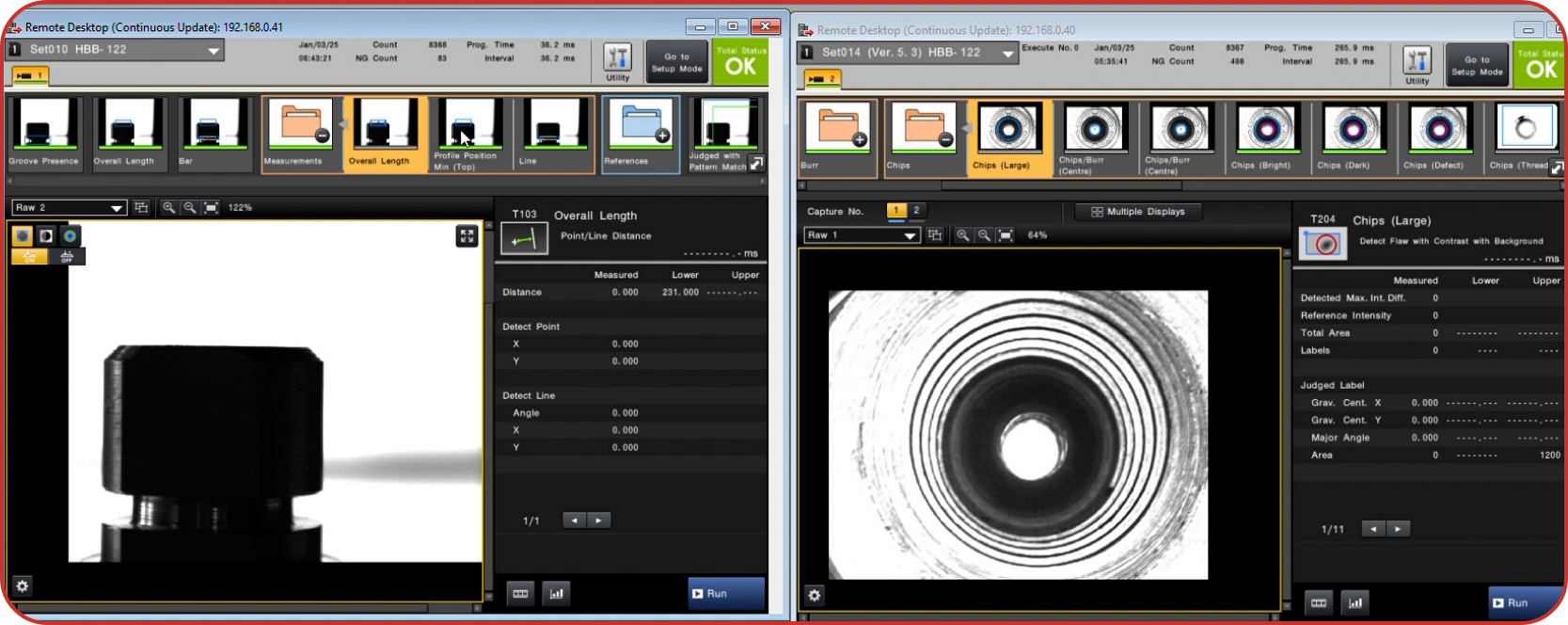
2. Predictive Maintenance
Vision systems collect vast amounts of data—not just on product quality, but also on machine behavior. Using analytics and machine learning, this data can help predict when a component in the machine is likely to fail. Scheduled maintenance can then be performed before problems occur, saving time and money.
3. Enhanced Traceability
Every inspected part can be tagged with data—timestamp, inspection results, defect type, and more. This information can be linked with ERP or MES systems, creating a full digital record. In regulated industries like automotive or aerospace, this level of traceability is essential for compliance and product recalls.
4. Scalability and Flexibility
IoT-enabled systems are modular and scalable. As production lines expand or evolve, integrating new vision stations or adjusting inspection parameters can be done remotely and dynamically, without overhauling the entire setup.
Implementation Strategies
To fully benefit from this integration, manufacturers must consider:
• Data Compatibility: Ensuring that the vision system can communicate with existing software (e.g., OPC UA, MQTT, REST APIs).
• Cloud or Edge Processing: Deciding whether data should be processed on-site (edge) or in the cloud, depending on latency needs and data sensitivity.
• Cybersecurity Measures: Protecting sensitive inspection data and machine interfaces from breaches is critical in a connected environment.
• Training and Support: Investing in user-friendly interfaces and proper training ensures that operators can leverage the technology effectively.
Use Case Example: Sorsys RT-Series
The RT-306, designed for multi-angle inspections using up to six cameras, already supports modular design and AI-based inspection. Its architecture allows seamless integration with factory systems, making it an ideal candidate for smart manufacturing environments. Combined with the right camera resolution—matched to part size and defect type—it becomes a powerful tool for intelligent quality control.
Conclusion
The convergence of vision inspection technology with Industry 4.0 and IoT is not just a trend—it’s the new standard. Companies that embrace this shift will gain significant advantages in speed, efficiency, and quality. Sorsys Technologies, with its cutting-edge inspection machines, is well-positioned to help manufacturers lead this transformation.