Revolutionizing Die Casting with Advanced Vision Inspection Systems
The die-casting industry, known for producing high-precision, complex metal parts, has long been a cornerstone of manufacturing in sectors such as automotive, aerospace, and electronics. As demand for high-quality, defect-free products continues to rise, so does the need for advanced technology to ensure quality and efficiency. Enter advanced vision inspection systems a revolutionary tool transforming the die-casting process by enhancing precision, reducing defects, and improving overall production quality.
What is Die-Casting?
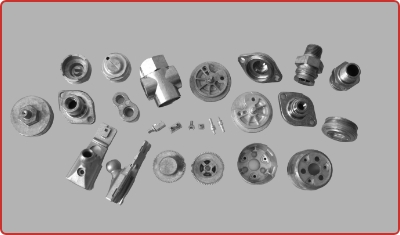
Die-casting is a manufacturing process in which molten metal is injected into a mold under high pressure to create parts with intricate shapes and tight tolerances. It is often used for producing parts that are lightweight yet durable, such as engine components, housings for electrical devices, and automotive parts.
Traditionally, die-casting manufacturers have relied on manual inspection, X-ray systems, and other conventional methods to detect defects in cast parts. While effective, these methods are time-consuming, prone to human error, and often unable to detect all types of defects. With increasing production demands and the push for higher quality standards, the industry is turning to automated solutions particularly advanced vision inspection systems to meet these challenges.
What Are Vision Inspection Systems?
Vision inspection systems utilize cameras, sensors, and sophisticated software to inspect parts in real-time during or after the manufacturing process. These systems can detect surface defects, measure dimensions, and verify the integrity of cast parts, providing manufacturers with a powerful tool for quality control.
The technology typically consists of high-resolution cameras paired with advanced image processing algorithms that can identify subtle imperfections such as cracks, porosity, surface roughness, and dimensional inaccuracies.
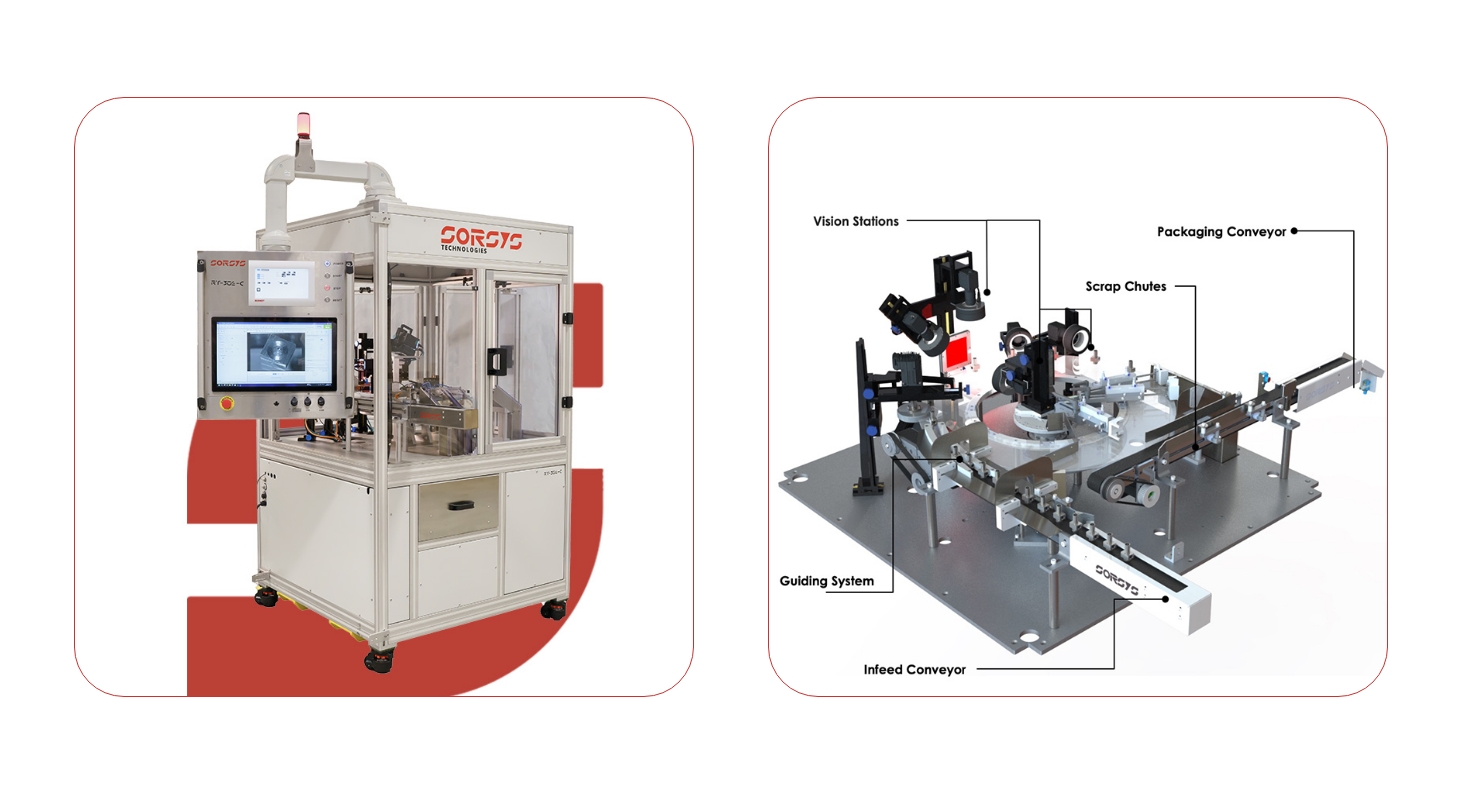
These systems can be integrated into the die-casting process, allowing manufacturers to monitor production without interrupting workflows.
How Vision Inspection Systems Revolutionize Die-Casting
Improved Quality Control
One of the main benefits of advanced vision inspection systems is their ability to perform real-time, non-destructive testing on cast parts. These systems can detect issues that might be invisible to the human eye, such as blister, tool damage, poor fill, internal voids, fine cracks, or tiny porosities.
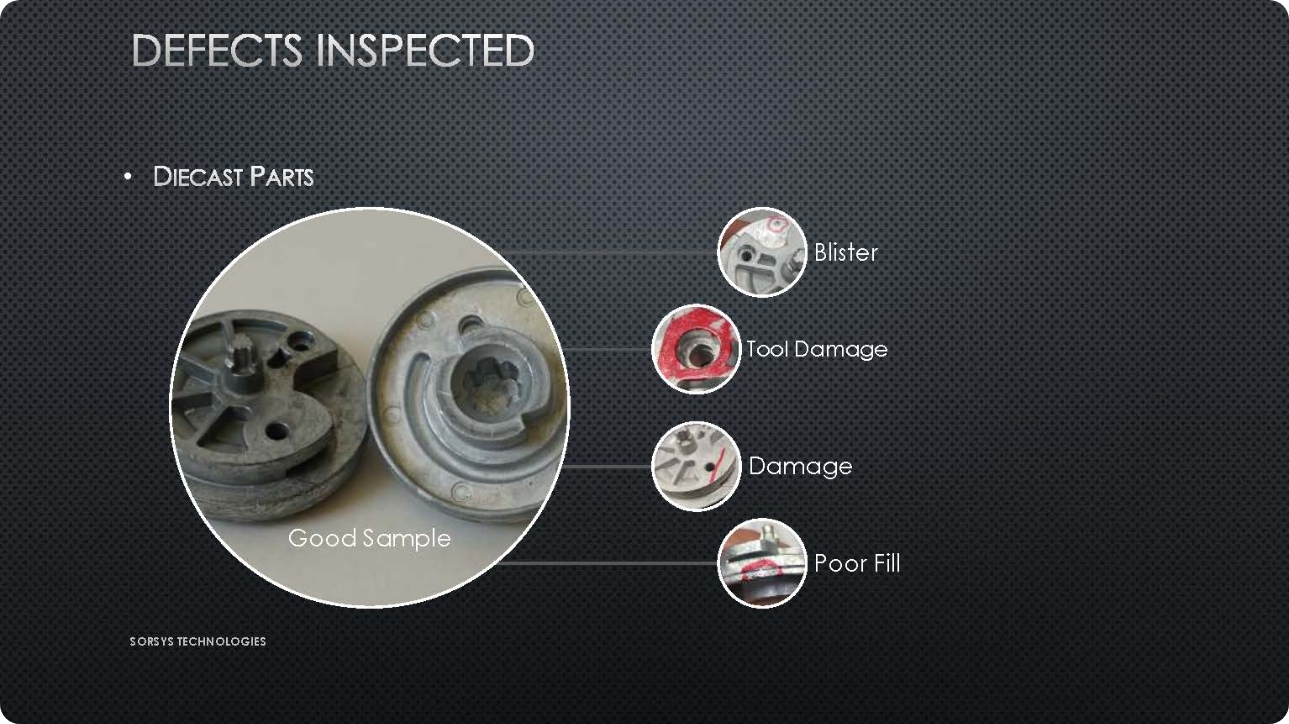
Traditional inspection methods, like X-rays, while effective, can be costly and time-consuming. Vision systems, on the other hand, provide faster feedback, reducing the likelihood of defective products reaching the assembly line or customers.
Vision systems also offer automated quality control, which eliminates the inconsistencies and subjectivity associated with manual inspections. This not only improves the reliability of inspections but also leads to higher product quality with fewer defects.
Faster Production Speeds
In die-casting, speed is crucial, especially in industries like automotive manufacturing, where high volumes of parts must be produced in short time frames. Traditional inspection methods often require parts to be removed from the production line, inspected off-line, and then reintroduced into the workflow. This can create bottlenecks and delays.
Vision inspection systems streamline this process by allowing parts to be inspected while still on the production line, without interrupting the flow of work. The rapid feedback provided by these systems means that manufacturers can detect problems early in the process, preventing costly delays and enabling faster production rates. Additionally, these systems can operate 24/7, further increasing throughput.
Enhanced Precision and Accuracy
Die-casting is a high-precision process, and even the smallest defects can lead to significant performance issues in end products. Advanced vision inspection systems provide unmatched precision in detecting defects and measuring the dimensions of parts. For example, some systems use 3D imaging to create highly detailed scans of the surface of a part, allowing for the detection of even the most subtle deformities.
This level of accuracy is particularly beneficial in industries like aerospace, where parts must meet stringent safety standards. In these applications, any defects could be catastrophic, and ensuring the integrity of each part is crucial.
Real-Time Data and Analytics
The integration of vision inspection systems with advanced data analytics software allows manufacturers to gather valuable insights in real time. The data collected from inspections can be used to monitor trends, identify recurring issues, and provide actionable insights for process optimization. This data-driven approach can lead to smarter decisions about equipment maintenance, material selection, and process parameters, further improving the overall efficiency and quality of production.
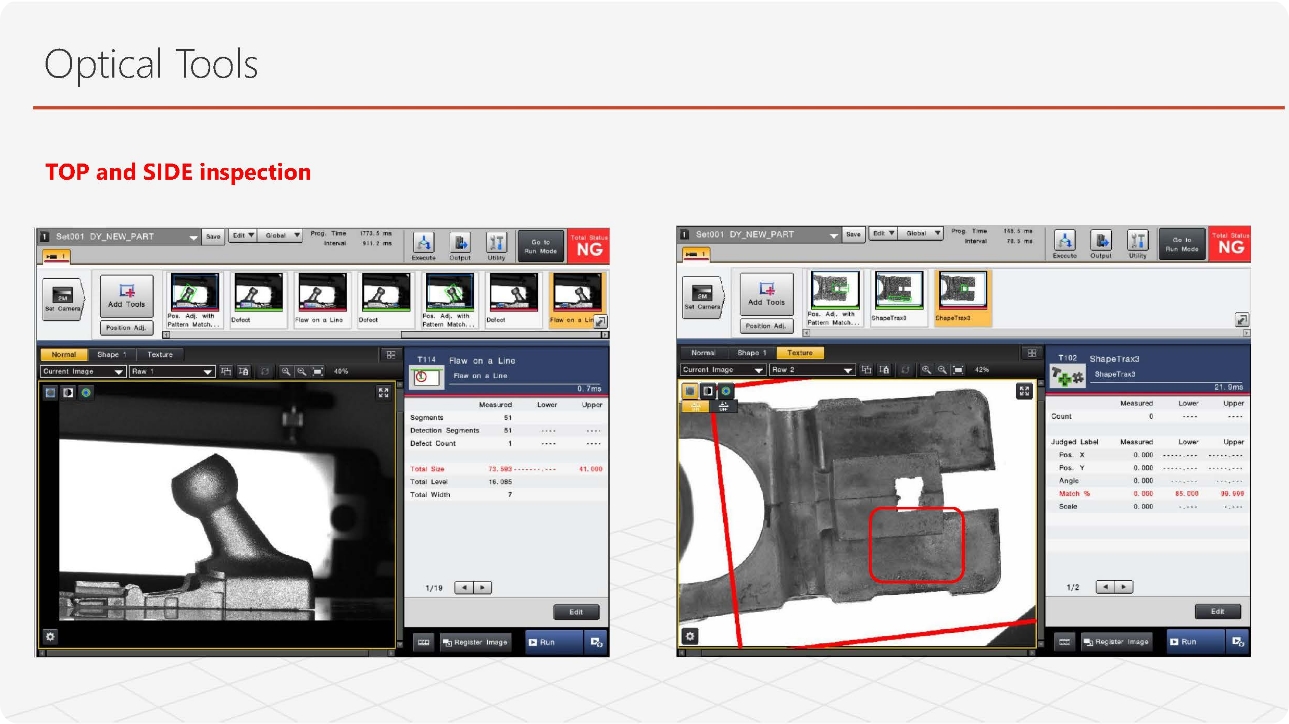
With predictive analytics, manufacturers can anticipate potential failures before they occur, allowing for pre-emptive adjustments to the production process. This helps reduce downtime, lower production costs, and prevent defects before they escalate.
Cost Savings and ROI
While the initial investment in vision inspection systems can be significant, the long-term savings often outweigh the costs. By reducing the number of defective parts, decreasing the need for rework, and improving overall production efficiency, these systems lead to substantial cost savings.
Moreover, the ability to monitor processes in real time allows for more efficient use of resources. Manufacturers can adjust machine settings, tooling, or material inputs to reduce waste, ultimately contributing to greater profitability.
Enhanced Flexibility and Scalability
Advanced vision inspection systems can be customized and adapted to suit the specific needs of different die-casting applications. Whether it's inspecting aluminum, zinc, or magnesium castings, these systems can be calibrated to detect defects unique to each material. Furthermore, as manufacturers scale up production or diversify their product offerings, vision inspection systems can be easily integrated into new production lines or used for different product types.
Challenges and Considerations
While vision inspection systems offer many advantages, there are also challenges that manufacturers must consider. For instance, the quality of the cameras, sensors, and lighting conditions can impact the accuracy of inspections. Moreover, the complexity of the software algorithms may require skilled personnel for calibration and maintenance.
The cost of implementing these systems can also be a barrier for small- and medium-sized enterprises (SMEs), although the declining cost of sensors and cameras, coupled with the ongoing development of more user-friendly software, is helping to make these systems more accessible.
The Future of Die-Casting with Vision Inspection Systems
As the die-casting industry continues to embrace automation and Industry 4.0 technologies, vision inspection systems will likely play an even greater role in driving innovation and efficiency. The continued advancement of artificial intelligence (AI) and machine learning (ML) algorithms will further enhance the capabilities of these systems, allowing for more advanced defect detection, process optimization, and predictive maintenance.
Additionally, as global competition increases, the need for consistent, high-quality production will become even more critical. Vision inspection systems offer a clear path forward in meeting these demands, ensuring that manufacturers can produce complex die-cast parts with the precision and quality required for modern applications.
In conclusion, the integration of advanced vision inspection systems into the die-casting process marks a transformative shift in the industry. These systems enhance product quality, streamline production, and provide valuable insights into the manufacturing process, all while reducing defects and costs. As technology continues to evolve, the potential for vision inspection systems to revolutionize die-casting is boundless, helping manufacturers stay competitive in an increasingly demanding market.
Sources:
• "Advancements in Die Casting and Inspection," Foundry Management & Technology.
• "Machine Vision Systems: The Future of Manufacturing Inspection," Vision Systems Design.
• "Benefits of Machine Vision in Die-Casting," Automation World.