How Automation Transforms Industrial Machines for Cost Savings and Efficiency
The Importance of Quality Control in CNC Manufacturing and the Role of Automated Feeders and Inspection Systems
In the world of manufacturing, particularly with CNC (Computer Numerical Control) machinery, quality control is paramount. It ensures that each product meets stringent standards for accuracy, durability, and performance, minimizing costly errors and maximizing customer satisfaction. Advanced technologies are reshaping this landscape, with robotic feeders and inspection machines now playing critical roles. Automated feeding of CNC machines and post-production inspection systems enhance not only efficiency but also the consistency of manufactured parts.
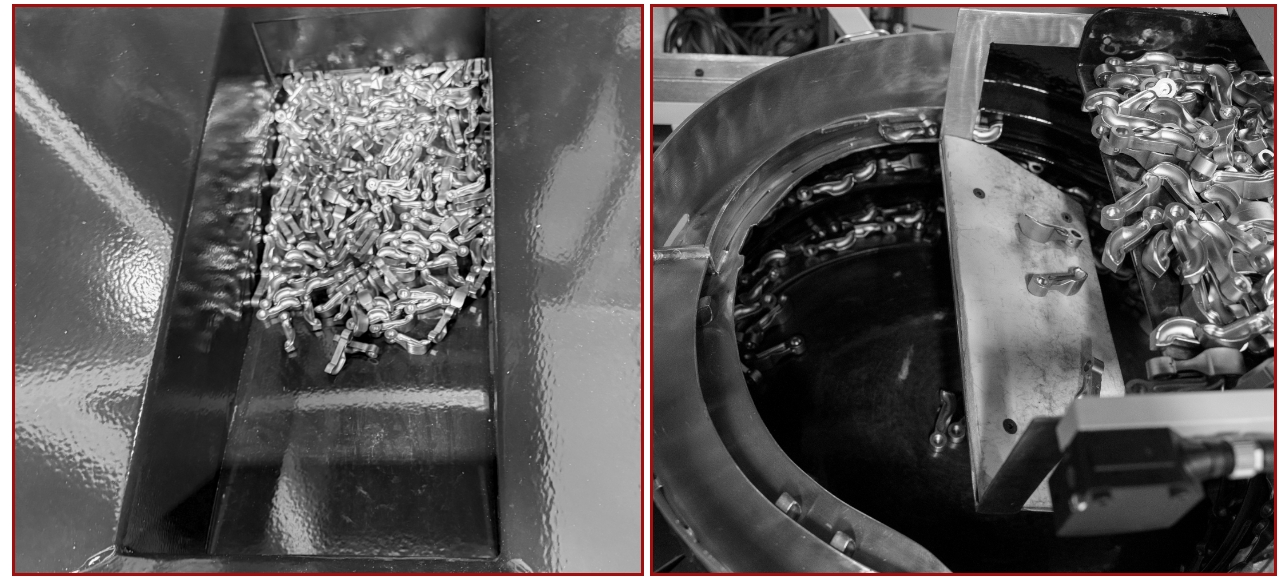
Quality Control and Its Importance in CNC Manufacturing
CNC machines are renowned for their precision, but the potential for defects can arise during material feeding, machining, or handling of parts. Quality control (QC) mitigates these risks, ensuring each component meets the design specifications required for assembly, safety, and performance. In industries like aerospace, automotive, and medical manufacturing, QC is not just a preference but a necessity, where any minor defect could have significant consequences.
Traditional quality control can involve manual checks or basic inspections, which are often time-consuming and subject to human error. Automated inspection systems, however, use advanced sensors, cameras, and AI-driven software to detect defects such as dimensional inaccuracies, surface irregularities, and contaminants in real-time. This technological leap is revolutionizing QC, reducing errors and ensuring consistency in parts produced by CNC machines.
Automating CNC Feeding with Robots
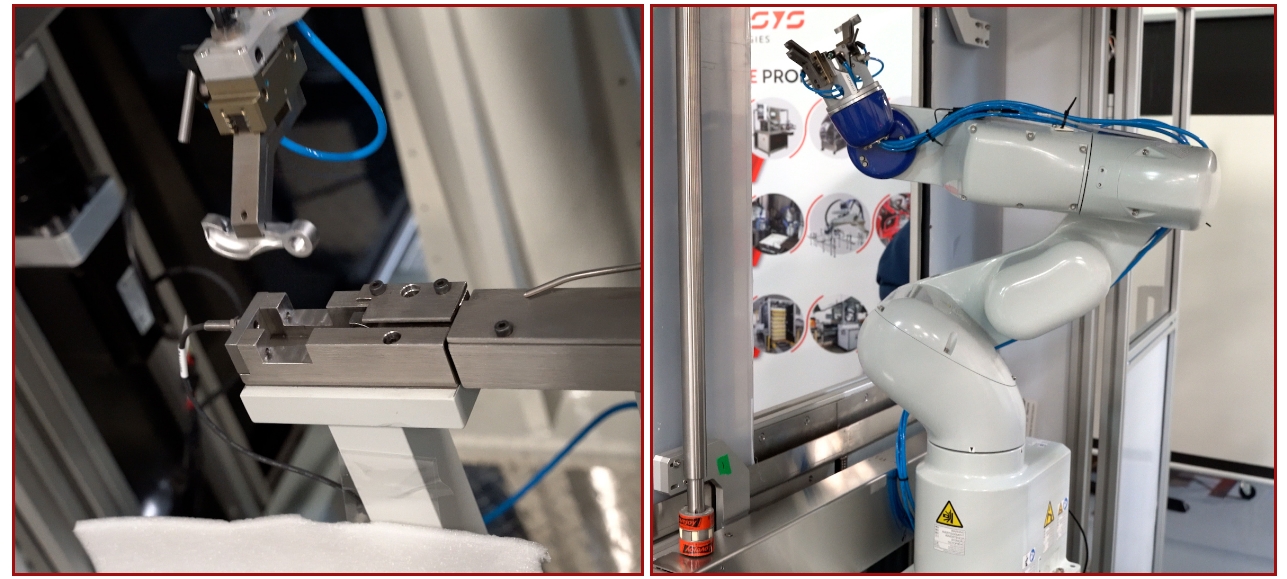
In many production lines, CNC machines need a steady stream of materials, either raw or semi-finished, to maintain productivity. Manual feeding requires consistent human intervention, which can be costly, inefficient, and prone to errors. Automated feeders solve this challenge, improving the reliability and speed of CNC operations by providing a constant, precise material feed.
Robotic feeders integrate seamlessly with CNC machines, managing the positioning and alignment of parts, and ensuring continuous operation. With robots handling material feeding, companies can save on labor costs, increase output, and reduce downtime. Furthermore, robotic feeders work at a consistent speed, which enhances machine performance and reduces wear on CNC components. These feeders are flexible and can adapt to various types and sizes of materials, accommodating production changes more easily than manual feeding systems.
Inspection Systems for Post-CNC Quality Assurance
Once a CNC machine has finished creating or modifying a part, a quality inspection machine can take over. Inspection systems, such as Sorsys Technologies' custom machines, employ high-resolution imaging, sensors, and AI algorithms to assess each component. They can detect defects like missing features, burrs, surface damage, dimensional issues, and contamination, all of which could compromise product performance or lead to costly recalls.
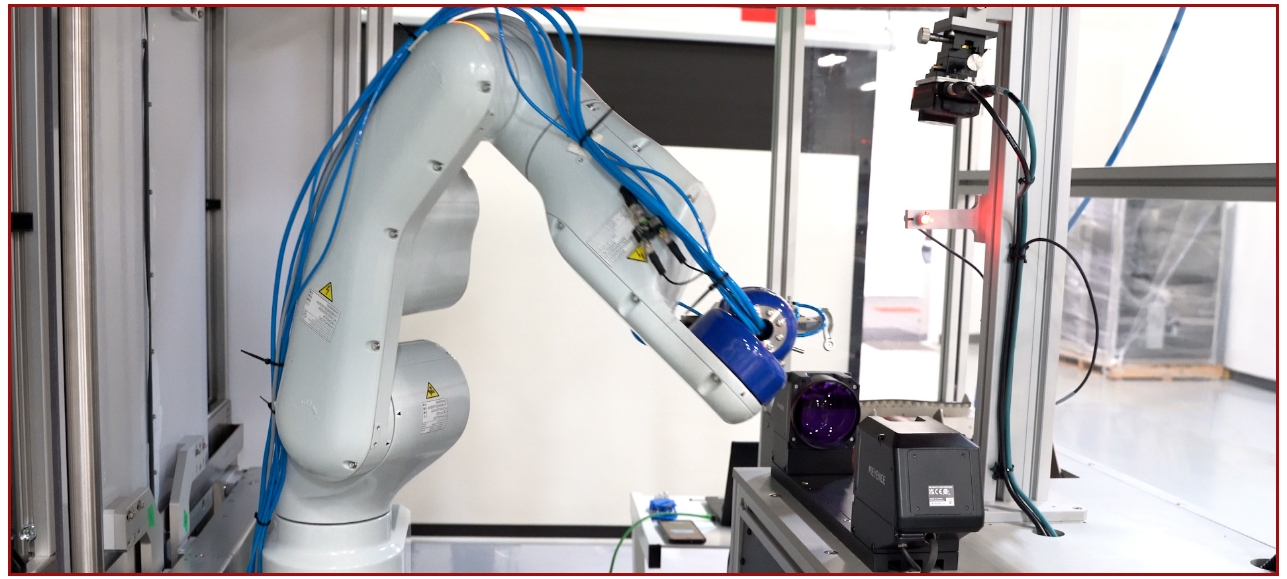
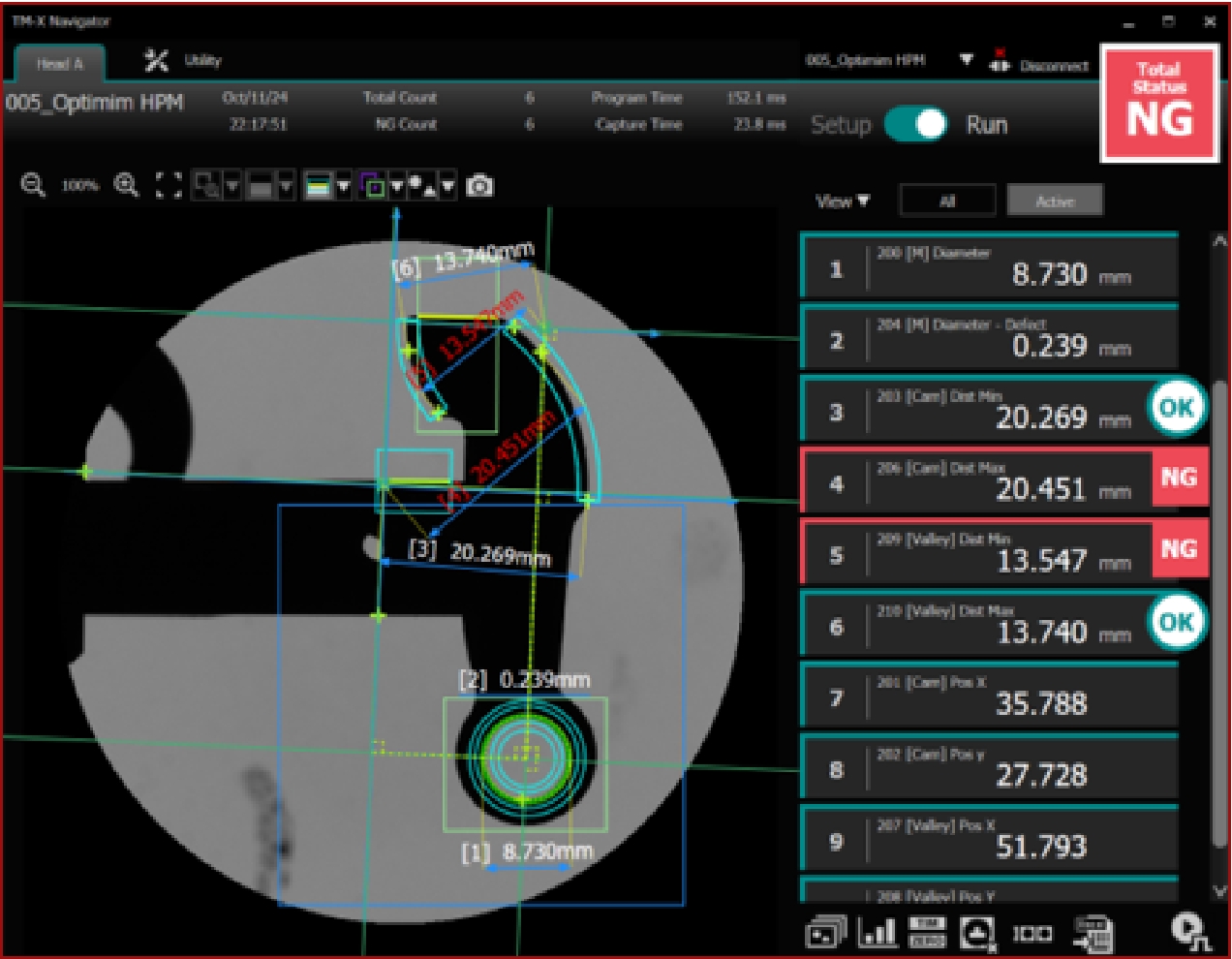
Sorsys Technologies’ inspection machines are capable of detecting defects in real-time and immediately identifying parts that don’t meet specifications. By doing so, they allow manufacturers to address issues promptly and maintain strict quality standards. Moreover, the data collected by these systems can be used for continuous improvement, helping to pinpoint recurring issues and refine processes over time.
CNC Automation and Quality Control: A Combined Approach
Integrating automated feeders and inspection systems is a game-changer for quality control in CNC production. With robotic feeders ensuring consistent material supply and automated inspection catching any post-production issues, manufacturers can achieve a closed-loop quality assurance process. This integration minimizes human intervention, reduces production costs, and enhances accuracy, leading to a higher-quality end product and more reliable production lines.
For manufacturers looking to stay competitive, automation offers significant benefits. Companies like Sorsys Technologies provide turnkey solutions for CNC automation, offering not only feeders but also inspection systems that detect potential issues before products reach the customer. With innovations like these, the future of CNC manufacturing looks increasingly efficient, precise, and cost-effective.
Vision-Guided Robotics: Revolutionizing Industrial Automation and Cost Efficiency
Vision-guided robotic (VGR) systems represent a significant leap in automation by incorporating cameras and sensors to guide robots in complex tasks such as inspection, assembly, and material handling. These systems, which integrate machine vision with robotic capabilities, can adjust to dynamic environments, offering significant advantages over traditional robots and human labor.
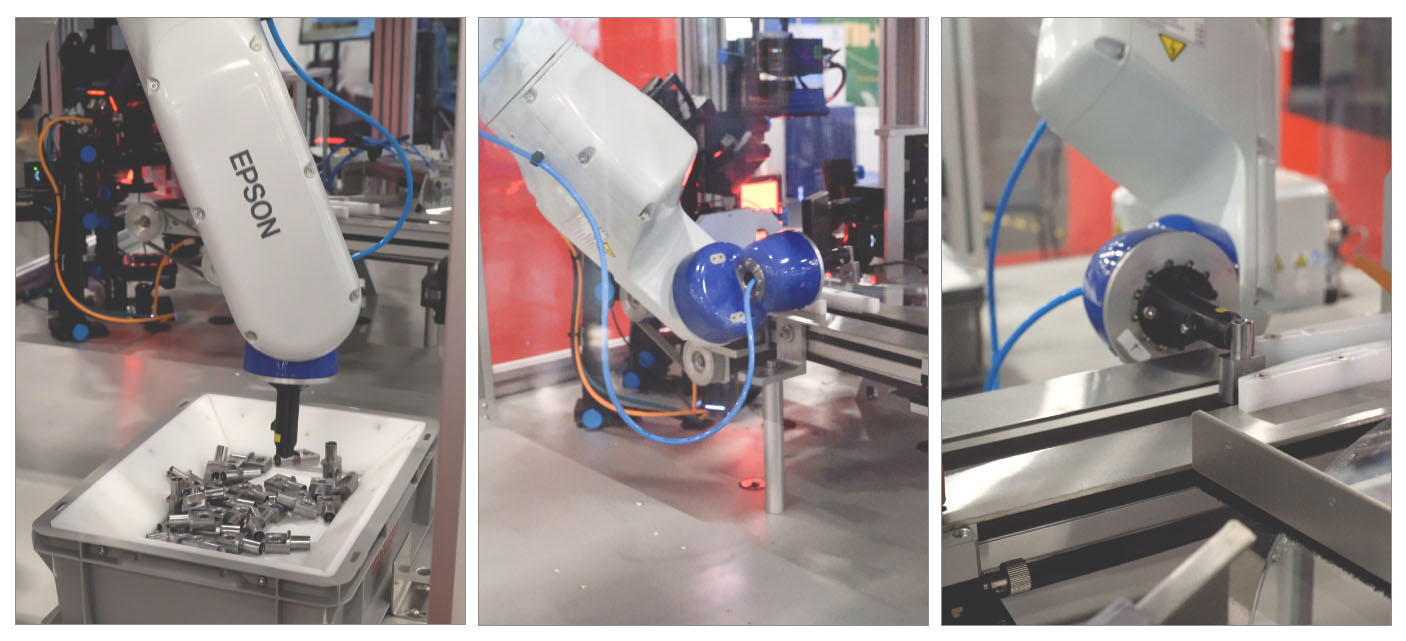
Advantages of Vision-Guided Robotics Over Human Labor
1. Accuracy and Speed: Vision-guided robots consistently deliver higher accuracy than humans, especially in repetitive tasks. Unlike human workers, robots do not experience fatigue, resulting in consistent precision and operational speed. They are particularly beneficial in industries requiring tight tolerances and high-speed production.
2. 24/7 Operation: Robots can work around the clock without breaks, allowing companies to operate multiple shifts. This leads to increased output and quicker payback on the initial investment, while humans require regular breaks and cannot work continuously.
3. Reduction in Errors: Human workers are prone to fatigue, which can lead to costly mistakes, particularly in tasks requiring repetitive actions. Robots, guided by vision systems, execute tasks with near-perfect accuracy, reducing waste and improving quality control.
4.
Labor Savings: A typical human worker might cost a company around $45,000 annually, excluding benefits. By automating tasks traditionally performed by two human workers per shift, a company can save about $90,000 per year per robotic system. Over a robot's lifespan, this leads to significant cost reductions (
Automate)
Cost of Implementing Vision-Guided Robotics
The cost of a vision-guided robot varies depending on complexity and functionality. A basic collaborative robot (cobot) with vision capabilities can start at around $35,000. High-end robots, with advanced features for specialized tasks like inspection, might cost upwards of $100,000
However, the benefits quickly outweigh the costs, with many businesses recovering their investment within 1-2 years. For instance, a $250,000 robotic system can generate over $1.5 million in savings within 7-10 years through labor reductions, enhanced productivity, and improved quality control (
Automate).
Potential Savings and ROI
The savings from switching to robots can be immense. For example, a typical vision-guided robot working two shifts can reduce labor costs by up to $90,000 annually. Given the low maintenance costs (as little as $500 per year in the first few years), these systems are not only reliable but also financially sustainable in the long run(
Automate).
Additionally, robots reduce downtime caused by human errors or fatigue, leading to improved productivity.
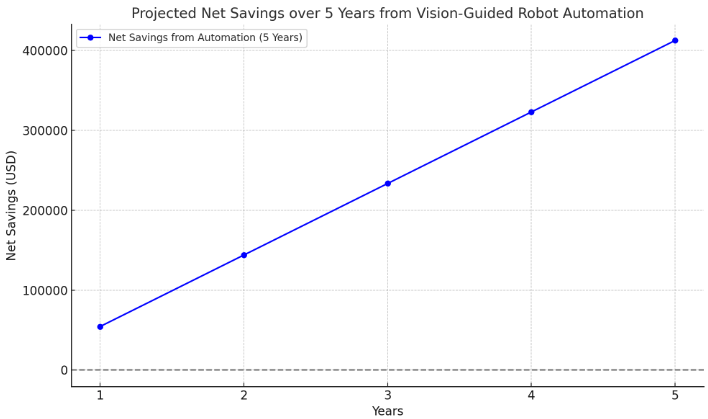
Conclusion
While the initial cost of vision-guided robotic systems might seem high, their ability to deliver precise, 24/7 operations makes them highly cost-effective compared to human labor. They drastically reduce labor costs, improve product quality, and provide a strong return on investment within just a few years, making them an attractive option for businesses looking to scale their automation capabilities.
Automation is reshaping the industrial landscape, driving unprecedented
Revolutionizing Industry: How Automation Transforms Industrial Machines for Cost Savings and Enhanced Efficiency
Automation is reshaping the industrial landscape, driving unprecedented changes in the way machines operate. By integrating advanced technologies, industrial machines are becoming smarter, faster, and more efficient, leading to significant cost savings and superior results. Here’s a closer look at how automation is transforming industrial machines and the myriad benefits it brings to businesses.
The Role of Automation in Industrial Machinery
Automation involves using control systems, such as computers and robots, to handle various processes and machinery with minimal human intervention. In the context of industrial machines, automation can range from simple mechanized tasks to complex, intelligent systems capable of making decisions and optimizing processes in real-time.
Key Benefits of Automation in Industrial Machines
Increased Speed and Efficiency:
Automated machines operate at speeds far beyond human capability. This increased speed translates directly into higher production rates. Additionally, automation minimizes downtime by performing continuous operations without the need for breaks or shift changes, ensuring that production lines run smoothly and efficiently.
Improved Accuracy and Precision:
Automation reduces the margin of error in industrial processes. Machines equipped with sensors and advanced control systems can execute tasks with pinpoint precision, ensuring consistent quality and reducing the likelihood of defects. This level of accuracy is particularly crucial in industries such as electronics, pharmaceuticals, and automotive manufacturing.
Cost Savings:
While the initial investment in automation technology can be substantial, the long-term savings are significant. Automated machines reduce labor costs by performing tasks that would otherwise require numerous workers. Moreover, automation minimizes waste and rework by maintaining high-quality standards throughout the production process, further driving down costs.
Enhanced Flexibility and Scalability:
Modern automated machines are highly adaptable and can be quickly reprogrammed or reconfigured to handle different tasks or product lines. This flexibility allows businesses to respond swiftly to market changes and customer demands. Scalability is also easier to achieve, as adding new automated units or upgrading existing ones is more straightforward than expanding a manual workforce.
Safety and Risk Reduction:
Automation takes over hazardous tasks, significantly reducing the risk of workplace accidents and injuries. By keeping human workers away from dangerous environments, businesses not only protect their employees but also save on potential compensation and downtime associated with accidents.
Data-Driven Insights:
Automated industrial machines often come with integrated data collection and analysis capabilities. These systems provide real-time insights into production metrics, equipment performance, and potential issues. By leveraging this data, businesses can make informed decisions, optimize processes, and anticipate maintenance needs, thereby preventing costly breakdowns and ensuring continuous operation.
Real-World Applications of Automation
Automotive Industry:
Automation has revolutionized car manufacturing, from robotic assembly lines to automated quality inspection systems. These innovations have drastically reduced production times and costs while enhancing the precision and reliability of vehicle components.
Food and Beverage Sector:
Automated machines in this industry handle everything from sorting and packaging to quality control and labeling. This not only speeds up production but also ensures compliance with stringent health and safety standards, reducing the risk of contamination and recalls.
Electronics Manufacturing:
In electronics, automation is critical for the precise placement of tiny components on circuit boards. Automated systems can perform these delicate tasks at speeds and accuracies unattainable by human hands, ensuring the high quality and functionality of electronic devices.
Pharmaceutical Industry:
Automation plays a crucial role in the pharmaceutical sector by ensuring the precise formulation, filling, and packaging of medications. Automated machines handle everything from mixing raw materials to labeling and inspecting finished products. This not only increases production speed but also maintains strict quality control, essential for compliance with regulatory standards and ensuring patient safety.
Conclusion
The integration of automation into industrial machines marks a new era of manufacturing excellence. By boosting speed, accuracy, and efficiency, automation drives significant cost savings and delivers better results. As industries continue to embrace this technological revolution, the future of manufacturing looks increasingly automated, efficient, and profitable. Investing in automation is not merely a trend but a strategic imperative for businesses aiming to stay competitive and thrive in the modern industrial landscape.
The Impact of AI on Automation in Industrial Factories Introduction
Artificial Intelligence (AI) is transforming the industrial landscape, especially in the realm of automation. As factories increasingly adopt AI-driven technologies, they are witnessing significant improvements in efficiency, productivity, and flexibility. This article explores how AI is revolutionizing automation in industrial factories and the implications of this transformation.
Enhanced Efficiency and Productivity
AI enhances the efficiency and productivity of industrial operations by optimizing processes and reducing downtime. Traditional automation relies on pre-programmed routines, which can be inflexible and limited in handling unexpected situations. AI, however, brings in capabilities such as machine learning, predictive analytics, and real-time decision-making.
Predictive Maintenance: AI-powered predictive maintenance systems analyze data from machinery to predict potential failures before they occur. By identifying and addressing issues proactively, factories can reduce downtime, extend the lifespan of equipment, and save on maintenance costs.
Process Optimization: AI algorithms can analyze vast amounts of data to identify inefficiencies in production processes. By continuously monitoring and adjusting operations, AI ensures optimal performance, reducing waste and increasing output.
Improved Quality Control
AI-driven automation systems enhance quality control by detecting defects and anomalies with greater accuracy than human inspectors. Machine vision systems, powered by AI, can inspect products at high speeds and with a level of precision that is unattainable for humans.
Defect Detection: AI can identify defects in products on the production line, such as cracks, deformities, or misalignments, ensuring that only high-quality products reach the market.
Consistency: By maintaining consistent production quality, AI helps factories meet stringent industry standards and customer expectations, thereby reducing the likelihood of recalls and enhancing brand reputation.
Flexibility and Adaptability
Traditional automation systems are often rigid and difficult to reconfigure for different tasks. AI enables a higher degree of flexibility and adaptability in industrial automation.
Adaptive Learning: AI systems can learn from new data and experiences, allowing them to adapt to changing production requirements. This adaptability is crucial in industries where product designs and customer demands frequently change.
Robotics: AI-powered robots can perform complex tasks that require dexterity and precision. They can be easily reprogrammed for different tasks, making them valuable assets in manufacturing environments where production lines need to be reconfigured quickly.
Enhanced Safety
AI contributes to improved safety in industrial factories by monitoring conditions and predicting potential hazards.
Worker Safety: AI systems can monitor factory environments to detect hazardous conditions, such as gas leaks, fires, or equipment malfunctions. By alerting workers and triggering automatic shutdowns, AI helps prevent accidents and ensures a safer workplace.
Collaborative Robots (Cobots): AI-driven cobots work alongside human workers, taking on dangerous or repetitive tasks. These robots are equipped with sensors and algorithms that allow them to operate safely in close proximity to humans, reducing the risk of workplace injuries.
Challenges and Considerations
While the integration of AI in industrial automation brings numerous benefits, it also presents challenges that need to be addressed.
Integration Complexity: Implementing AI solutions in existing systems can be complex and require significant investment in infrastructure and training.
Data Privacy and Security: The reliance on data for AI operations raises concerns about data privacy and security. Factories must ensure that sensitive information is protected from cyber threats.
Workforce Impact: The adoption of AI-driven automation may lead to job displacement. However, it also creates opportunities for workers to engage in higher-skilled roles that require oversight and management of AI systems.
Conclusion
AI is a game-changer for industrial automation, bringing unprecedented levels of efficiency, quality, flexibility, and safety to factories. As AI technologies continue to evolve, their integration into industrial automation systems will become increasingly seamless, driving the future of manufacturing towards greater innovation and productivity. By addressing the challenges and leveraging the benefits of AI, factories can stay competitive in a rapidly changing industrial landscape.